OFIL makes Power Line Inspections more efficient
OFIL Europe provides network operators with reliable, high-quality data to make sound maintenance decisions.
Overhead power lines are critical infrastructure which must be inspected periodically to safeguard electricity supply and to comply with regulatory requirements. The need for predictive maintenance, the ability to utilize the full capacity of the network, and mitigation of wildfire risks are additional reasons for regularly inspecting the power grid.
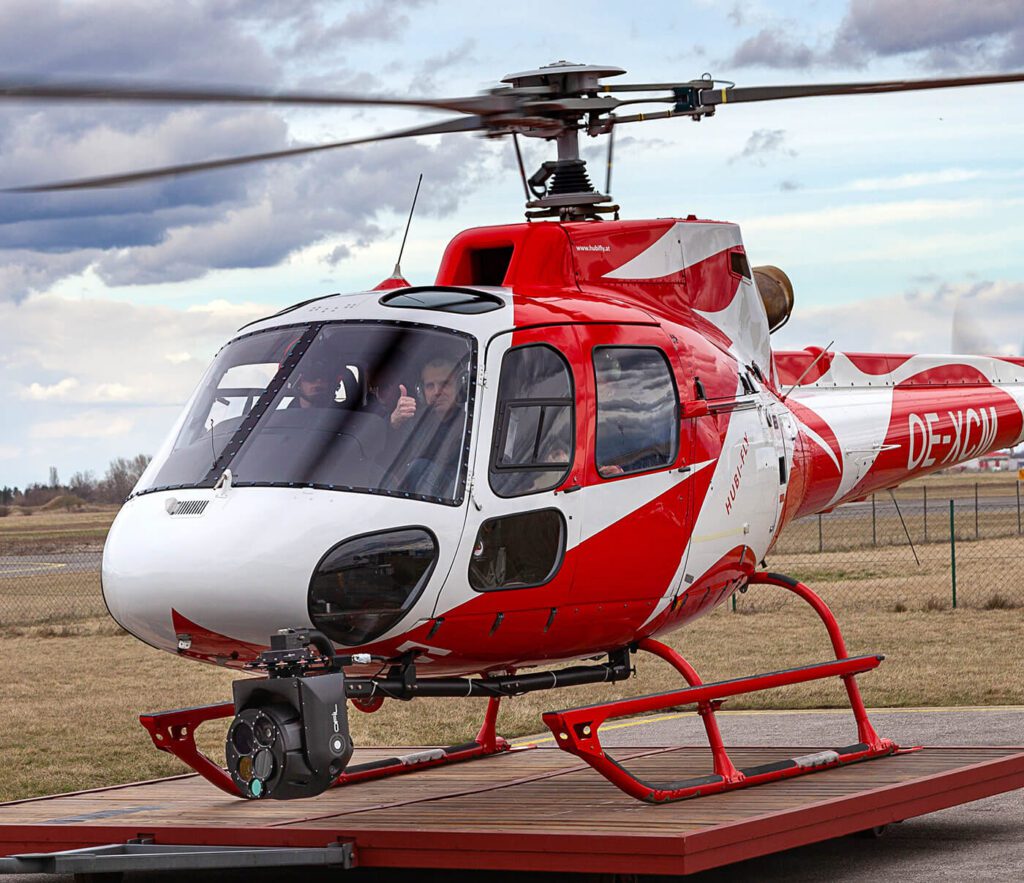
Scroll down to explore
When discussing inspection methods, the market is usually divided by platforms (patrols done on foot, ATV/SUV, helicopter, UAV/drone) and separated by the sensor technologies being used.
While various types of drones have emerged as a popular platform for rapid data collection in a small area, helicopters equipped with gyrostabilized multi-sensor inspection systems provide the most efficient method for large-scale missions doing hundreds of miles per day, every day.
Since there are various aerial inspection requirements for asset management there is no single solution to cover every need. Typically, utilities will use a combination of technologies and platforms.
Some major inspection categories are
Service support
Remote support and
service packages
maximize uptime in flight
Advanced Functions
Geo-lock/Auto steering/ Fault
Detection for
intelligent automation
Helicopter mounted
The ideal choice for the most
efficient long-distance power
line inspections with helicopter
platforms.
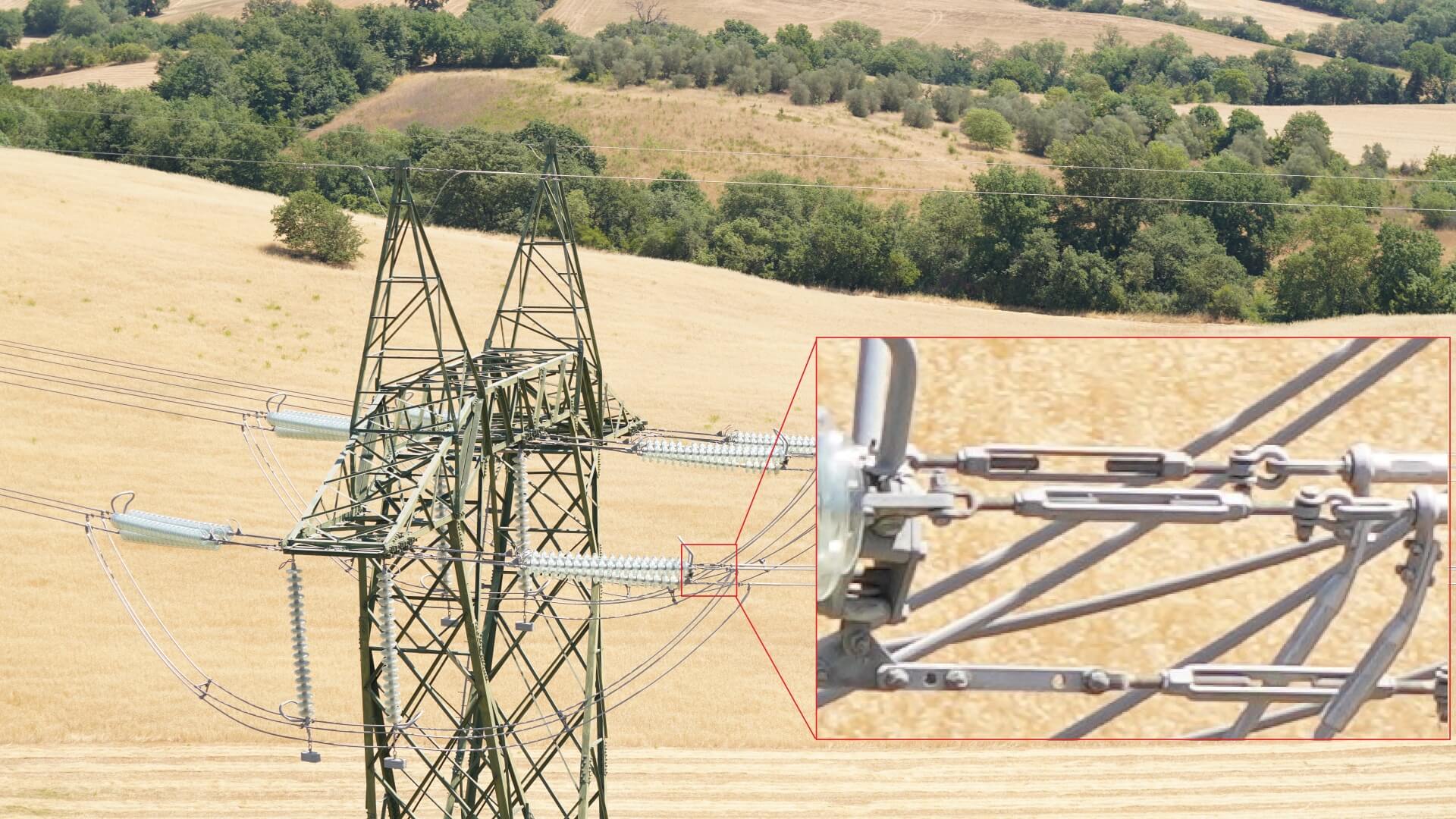
1. Visual Inspections
Visual inspections assess components, such as towers, insulators, conductors, and fittings, to identify signs of damage, wear, or abnormalities. Advanced imaging technologies, including stabilization, high-resolution cameras and powerful zoom capabilities, aid in capturing detailed visuals for further analysis.
Longer-range inspection solutions use high-end stabilization platforms, advanced zoom capabilities and imaging technologies to deliver high-res shots with pinpoint focus and beneficial viewing angles, keeping a safe distance while flying the lines. Findings can be seen online / in real-time, and decisions (for additional data acquisition or immediate action) can be taken promptly by experienced operators knowing what they are looking at.
2. Infrared Thermography
Infrared thermography utilizes specialized IR cameras to detect temperature variations along powerlines. Anomalies in temperature can indicate issues such as loose connections, broken or overloaded conductors, and faulty insulators.
While hotspots can be detected quite easily depending on the local conditions (line-loading, ambient temperatures, wind, etc.) precise temperature measurements of hotspots vs adjacent components are required to calculate the “Delta-T” or difference in temperatures, to estimate fault severity during reporting, before making costly maintenance decisions. This work is usually done by qualified and experienced thermographers in real-time, inspecting transmission networks with helicopters for thousands of miles.
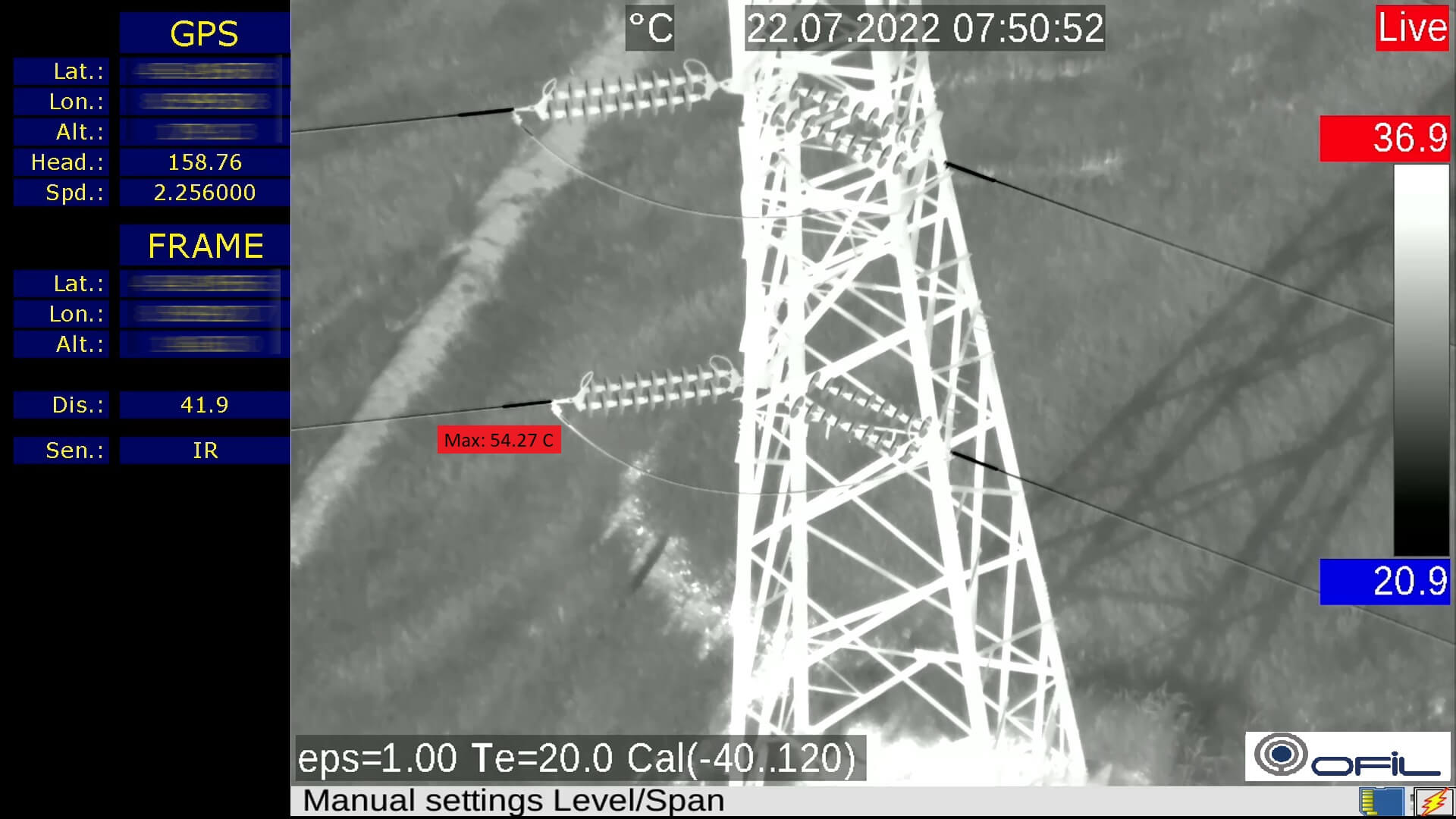
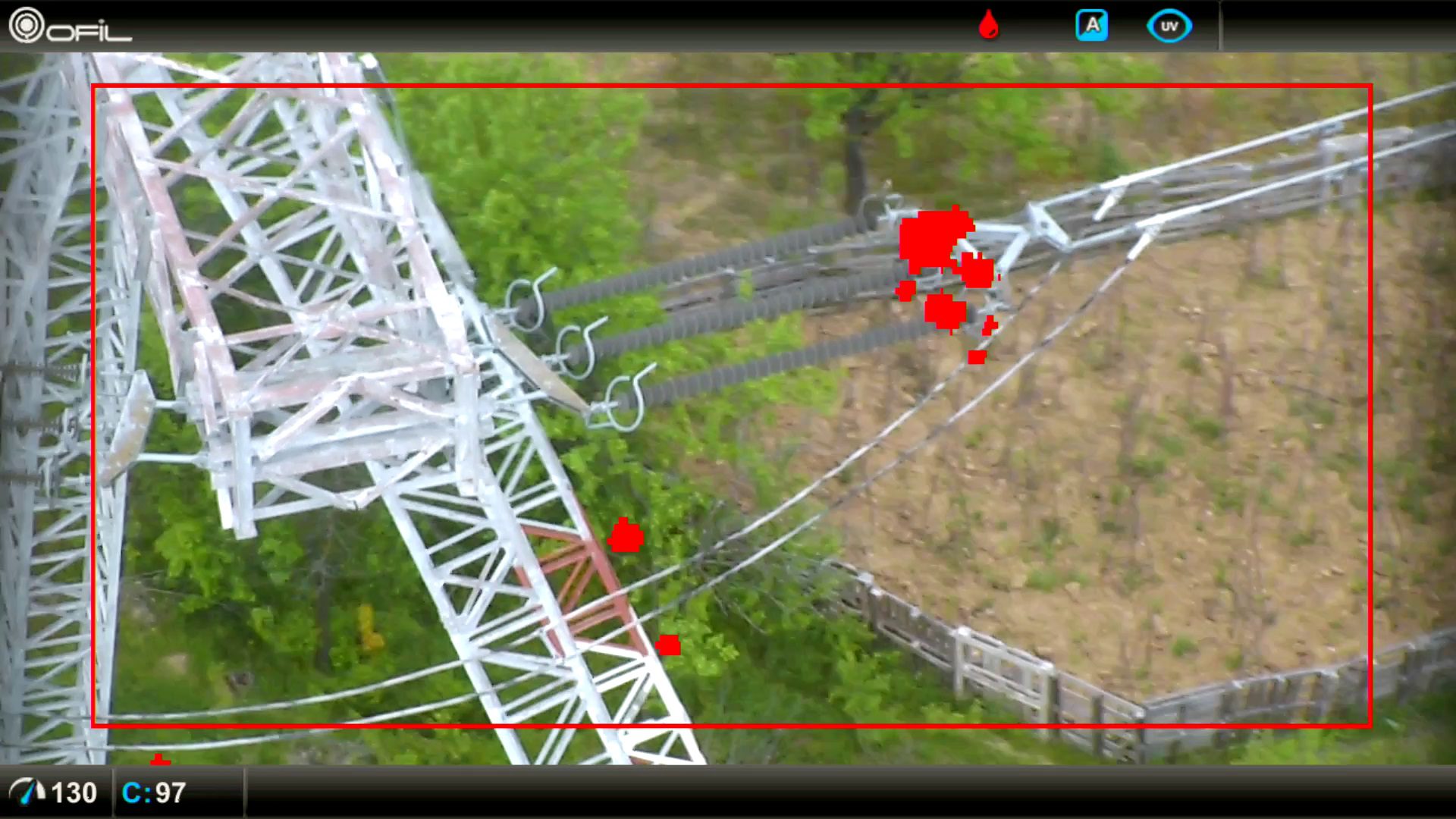
3. Ultraviolet (UV) detection
Corona discharge, also simply known as corona, is a phenomenon that occurs when high voltage powerlines create localised high electric fields due to – for example – defective components, causing ionisation of the surrounding air. Corona produces energy losses, increased RF noise, and damage to insulators, which can cause system failures and even wildfires.
Aerial UV inspections are complementary to IR since they find different types of faults, at different stages of failure. They also don’t need loaded lines or the same weather conditions. While Corona can be detected quite easily at fast inspection speeds, precise fault localisation and photon measurement for severity is typically done while hovering near the poles. Corona is often caused by compromised insulators, contamination, damaged conductors, loose connections or misaligned hardware.
4. LiDAR Scanning
LiDAR (Light Detection and Ranging) scanning employs laser sensors mounted on aircraft to generate highly accurate 3D models of the network infrastructure. This technology creates detailed point cloud representations, allowing for precise measurements and assessment of tower heights, conductor sag and vegetation clearances.
LiDAR scanning aids in identifying structural deformations, enabling timely repairs and maintenance. Usually, this inspection method is done using sensors mounted on fixed wing aircraft or helicopters, and increasingly also by drones. The data acquisition requires a different flight path and a constant height over the lines compared to other missions.
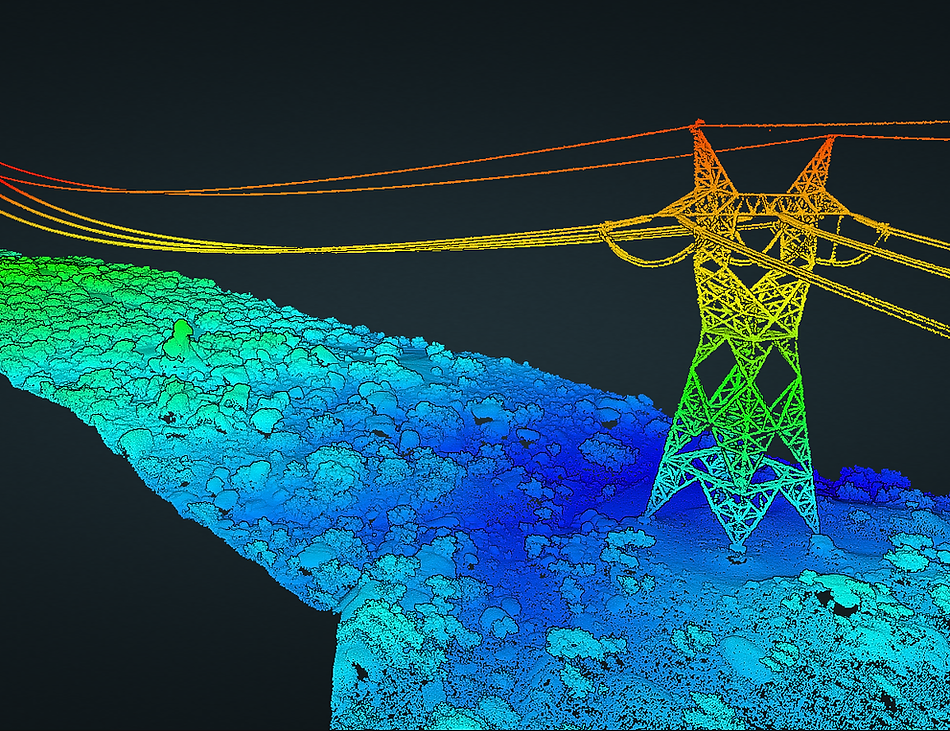
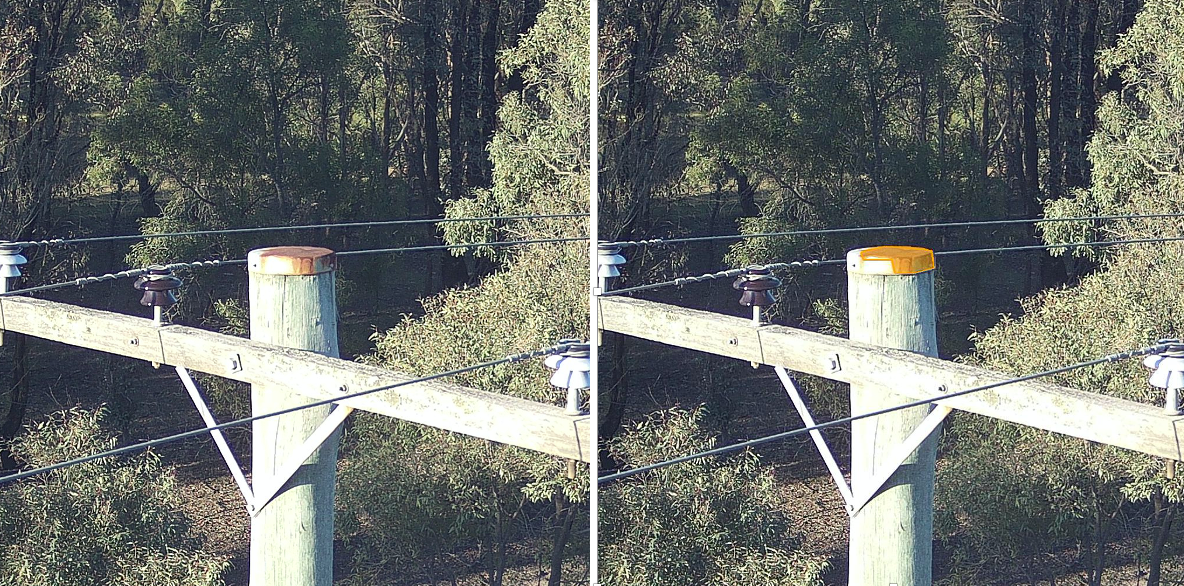
5. Corrosion Detection
Corrosion is a significant concern for powerline infrastructure, particularly in humid or coastal areas. Specialized inspection techniques, such as electromagnetic corrosion detection or pattern recognition help identify obvious or hidden corrosion within conductors or metallic components.
6. Component Mapping and Database Integration
Accurate mapping and database integration are crucial for effective powerline maintenance and management. Aerial inspections can be utilized to create comprehensive maps of all components within the power grid, facilitating better detection, monitoring, and storage of vital information. AI enhanced software helps to automate this process.
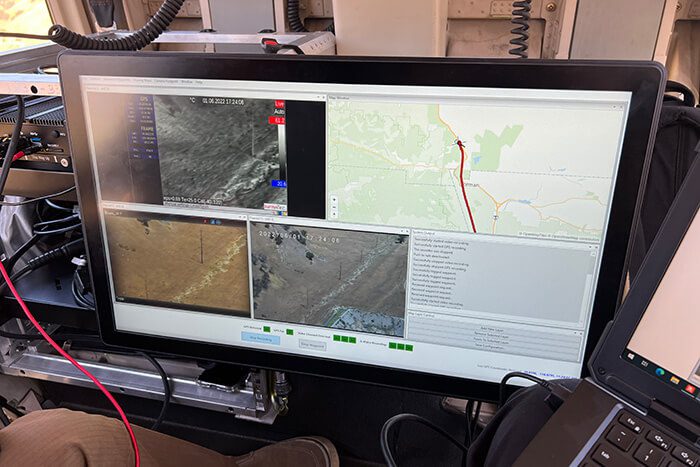
OFIL Europe benefits for the power line inspection market
Our mission is to provide the Energy sector with the most advanced inspection solutions available for power line inspection. From the hardware that collects dependable data at the highest level of precision, overall quality and consistent repeatability to advanced functions like incorporating artificial intelligence that streamlines the data acquisition process and automizes inspections for large scale networks and UAVs/Drones.
- OFIL Europe is the only developer of “Gyrostabilized Multisensor Gimbals” dedicated for airborne powerline inspection. Being part of the OFIL Systems Group we benefit from decades of knowledge in the energy industry and we understand the need for predictive maintenance.
- As a developer we are in close cooperation with our customers and partners to continuously deliver new capabilities and intelligent functions to existing and new systems. We configure payloads to their specific demands.
- Based on our bottom-up developed, leading edge system architecture we provide the highest inspection efficiency, with the end-users’ needs in mind.
- Precisely selected sensor packages + deep integration of all sensors provide ease of use to enable full dedication to the mission purpose in the visual, IR, and UV spectrums.
- As a result, we provide the highest measurement precision & data quality to find anomalies quickly and efficiently in real-time. Efficient reporting is supported in post processing.
Our Products
Our gyrostabilized multispectral gimbal systems are uniquely tailored to and optimised for power line inspections, benefiting from decades of OFIL’s experience in this market. They offer the highest spec’ed sensor options, including OFIL’s leading UV DayCor® technology.
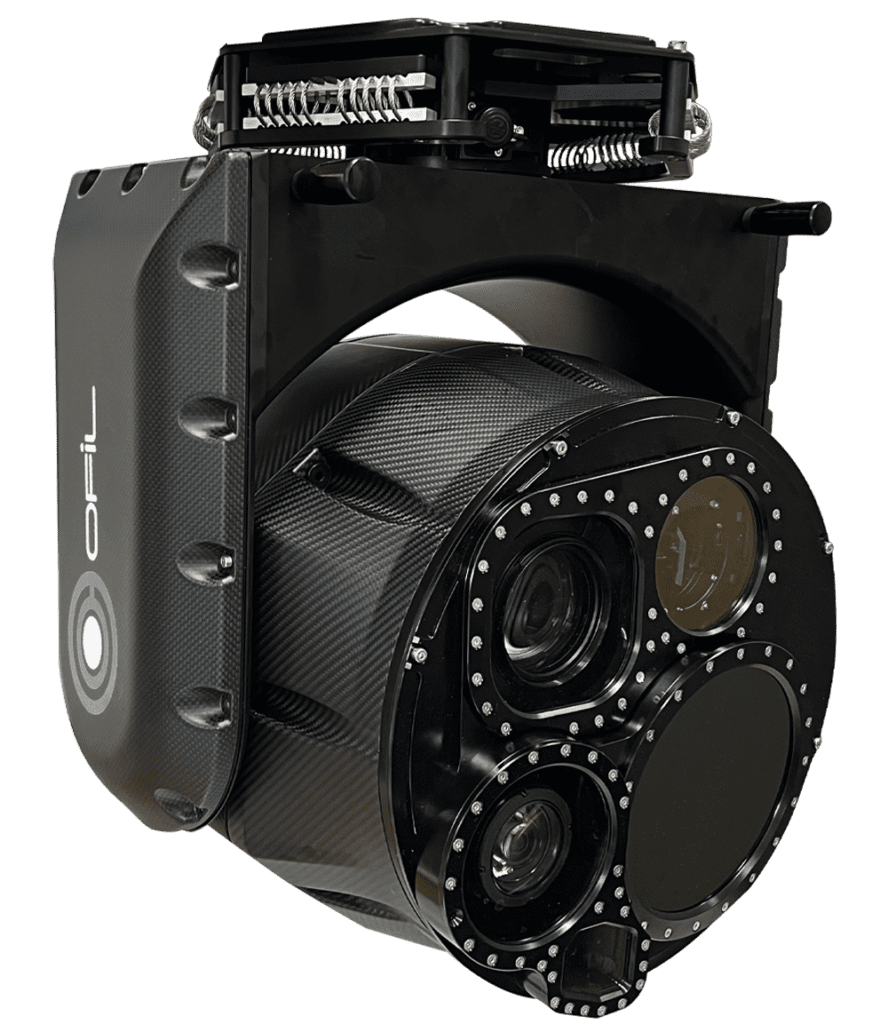
ROM Ultra
The highest spec’ed 5-sensor system with deep intergration of 4K Video/Radiometric Infrared HD Sensor, 120mm Lens/61MP Still Camera 140-400mm lens/OFIL’s high sensitivity UV HD Sensor/LRF and intelligent functions. The ideal choice for demanding expert users.
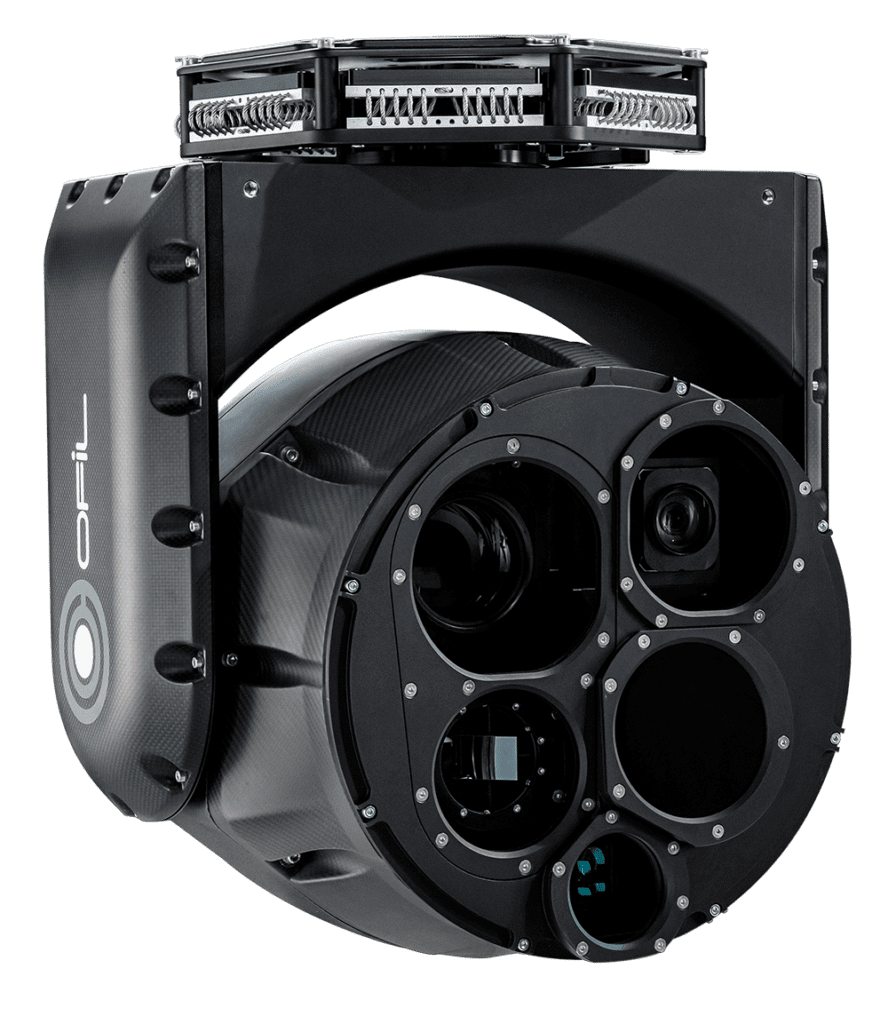
ROM HD
Our configurable precision product line incorporates 5-sensors, FOG (fiber optic gyro) technology for high performance drift-free gyrostabilization in 4 axis, and fiber optic technologies for pristine, low latency data transmissions. The ideal choice for inspections with various helicopter platforms.
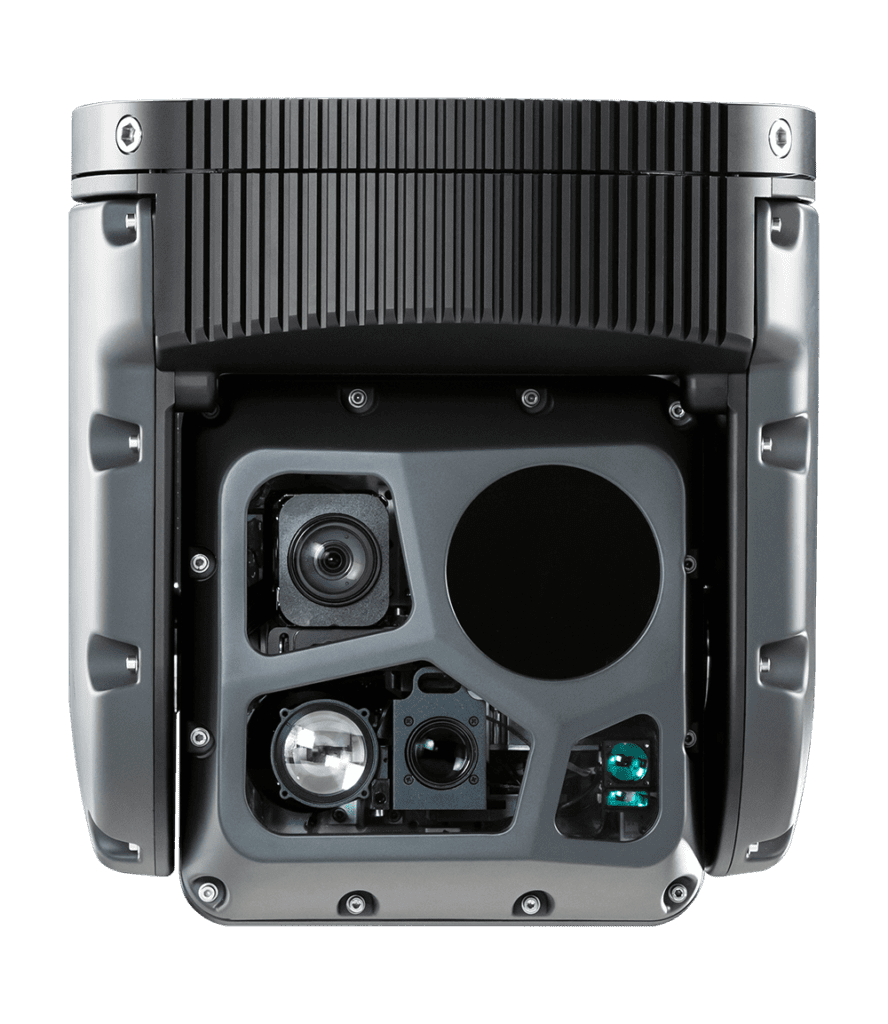
ROMLite HD
Compact, high precision 4-sensor system, including IR/UV/EO sensors in HD resolution, plus laser range finder. The ideal choice for inspections with lighter aircraft and heavy-duty UAVs/Drones.
FAQ
All aerial operations near power lines need special preparation and training to meet safety requirements, even more if the lines are loaded.
Today’s helicopter flight inspections are typically done 50-80 meters (150-250 feet) away from the lines; our powerful optics deliver high-res images and precise measurements without needing to get much closer.
Yes, all sensors are running concurrently, and the total mission is recorded in all video streams (EO/IR/UV) but depending on the focus of the inspection, the operator may choose to pay more attention to a single stream.
Yes, due to the deep integration of all sensors under one user interface it is common to fly the system with only one inspector. Due to the functionality, there is also the capability to have 2 or 3 inspectors on board, each focused on separate aspects.
Doing HD/4K videos and high resolution pictures from quite a distance and the need to capture the tiniest details , means you need strong zoom capabilities. This, and capturing the most precise measurements with IR and UV sensors, requires a perfectly stabilized system while operating from a vibrating helicopter platform.
A 4-axis stabilized gimbal system will cost several hundred-thousand dollars (or euros) depending on the sensor payload, flight recording capabilities, auxiliaries, and specialized functions.
5 axis stabilization of gimbals is used in the media business to eliminate the “role” in the video capture, which is unpleasant to watch in movies or documentaries. For utility gimbals this is not necessary and adds complexity and weight without any benefit.
Questions, enquiries and partnership opportunities
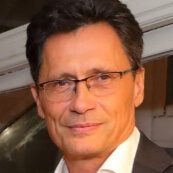